When Joe does what he likes to call loud gigs, Like touring with "Blue Beck"
or Lew Soloff's Food Group, he typically uses a solid body guitar to avoid
feedback. But he prefers the size, feel and sound of a hollowbody
instrument. |
|
Joe dropped off a production model of his signature guitar - a Cort Beck 6.
an instructed me to come up with a way of eliminating the feedback at high
volumes. Putting in a huge block was out of the question due to the
weight. Here is what we came up with. |

I asked Joe if he would mind us cutting a hole in the back of the guitar. |
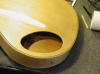
He said "You can cut it in half for all I care - just get it to stop
howling" |
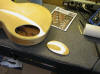
In these three pictures, you can see to hole
we put in the back of the guitar, you'll see why we did hat later |
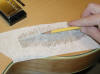
Next we moved to the front of the guitar and traced the sound holes. |
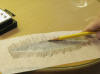
I used something called pre-mask tape.
It has a very low tack and is very thin - perfect for this job. |
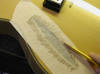
I am essentially taking a rubbing of the
cat's eye holes. We had to do both of them since they are not exactly
uniform. |
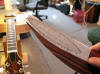
We then transferred our rubbing to a nice looking piece of rosewood. |
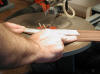
Using the tracing as a guide we cut out the
shape of the cat's eye on the scroll saw.
|
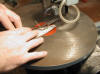
If you look close, I am not cutting right on
the line - more like just outside of it. |
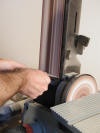
Next we step over to the large belt sander |
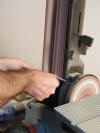
Here I am sanding right down to the line - I want a nice tight fit in the
holes so I make sure that I don't take off too much. |
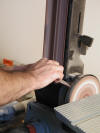
I also want a nice smooth finish with no
jagged edges. |
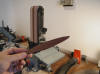
The finished part - let's see how it fits ... |
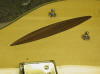
A nice snug fit ... |
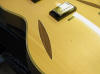
just enough to hold it from falling through
the hole but not so tight we can't pull it out. |
Joe asked us to make anything we do to be
removable in case he wanted to go back to a fully hollow instrument. So
merely gluing the inserts in was out of the question. So here is what
we came up with. |
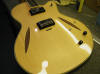
Here is the guitar wit the inserts in place. In order to make the inserts
removable without having to have a tool to take them out - we needed a
cover. |
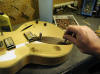
to make it look good we needed to have it
match the contour of the top of the guitar. So we used the guitar as a
sanding block |
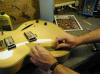
I glued a couple of dowels to the piece of
wood to make handling it easier. With some self stick sandpaper on the
guitar, he part matched the shape of the top in very little time. |
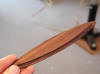
Next we glued the inserts to our new covers |
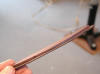
Only to cover needs to match the contour of
the top - however the inserts took the contour of the cover ... |
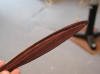
It's nice when things work out that way.
|
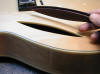
The new insert fits into the cat's eye very
nicely |
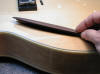
it merely slips into place and drops right
into the hole and it matches the contour of the face quite nicely |
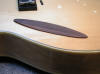
I was tempted to call this done - but I know
that this guitar is going to to a great deal of touring |
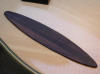
For a guitar that wasn't going to be handled
aggressively - the friction fit of these inserts would hold nicely |
Since I know that's not the case we are going
to have to come up with a way of securing them to keep them from falling out
- what we came up with does more than that - it actually helps stifle the
top even more. |
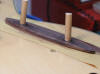
More on that a bit later - right now we have
one more insert to complete.
Here is a good look at the two dowels I quickly glued to the cover for easy
handling. |
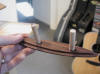
After shaping the cover to the face of the
guitar, I glued the insert to the cover and then glued the dowels to the
under side of the whole part. |
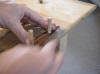
Using the dowels wasn't completely necessary
but it did make handling the whole piece a lot easier so it was worth the
little extra effort |
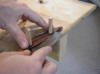
The second insert needed a bit more shaping -
so we trued it up with a nut ledge file. |
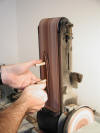
The dowels made working at the belt sander
much more comfortable |
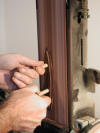
With much less risk of catching a finger or
losing control of the part. |
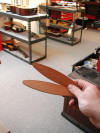
Here we have a couple of pieces of wood
shaped to match the cat's eyes, these will be the backing to mount the
covers to the sound holes. We actually decided to change the shape of
these for easier mounting - you'll notice that in a bit. |
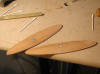
Inserted into each backing is a small
threaded nut to accommodate the knob that will be used to tighten the whole
plug system. |
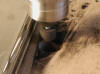
I wanted a good looking piece that
functioned with the turn of a knob but didn't want to use a large knob like
you would find on a volume control. So we turned our own knob. |
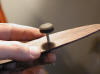
We mounted it directly to the threaded rod
that matched the 8/32 threaded nut inserted into the backing we made
earlier. The knob looks a bit rough in this picture - we cleaned them up
quite a bit for the finished product. |
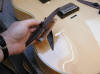
Here you can see how the insert works. |
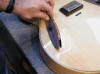
you slip the underside in the guitar at a
slight angle to seat the cover of the insert. |
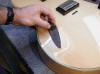
Begin tightening the knob to make the
underside swing perpendicular to the top of the insert. |
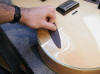
Continue tightening until the insert is nice
and snug - don't over tighten - just good and snug. |
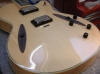
the idea here is not to merely fill the holes
but help restrict the tops movement a bit. |
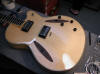
Here is another shot of both inserts in
place. By the way - the knobs are all cleaned up now. |
At this point you might be wondering why we
cut this big hole in the back of the guitar. You're about to find out.
Joe wanted a feedback proof guitar - I didn't think that sound hole plugs
would do it all on their own. |
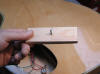
First we made a block of maple that matched
the inside curve of the back of the guitar just in the area where the bridge
would sit.
|
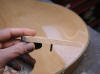
the block has a threaded insert that will
accept one end of a turnbuckle. |
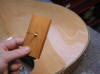
next we made one for the top. you can see
that it's a different material - I didn't bother matching the types of wood
- since this part is not coming in direct contact with the guitar |
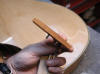
Both parts were made to fit in only one
direction so we were careful to make sure each part was marked appropriately |
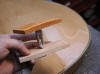
Here is the full assembly. The lighter
maple piece is for the back of the guitar and the mahogany will be on the
top. |
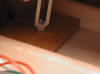
before we finish it up, I;ll double check the
fit of the curve inside the guitar. It fits just fine. |
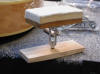
I chose to use a fairly thick piece of hard
felt for the top of the jack. This will stifle the to when tightened |
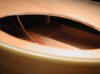
Here is a look at the insert in place.
The reason for the big hole is not just o put this part in - but it is
adjustable. |
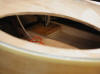
You can reach in the guitar, and loosen the
whole thing and the top part will release from the top of the guitar.
When you tighten it, it acts as a dampener for the top, restricting it's
movement |
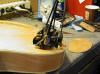
Here we are gluing inserts to attach the new
back plate. |
|
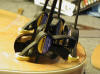
We can't just leave a huge hole in the back
of a guitar - can we? |
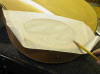
After that's done - we traced the hole in the
back of the guitar. |
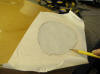
this is sign makers tape very thin -
very low tack. |
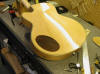
Our back plat is in place - screwed in like
the back plat on a Les Paul. I chose rosewood to match the rest of he
appointments on the guitar. |
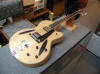
Here is a look at the finished product - all
strung up and ready. |
|
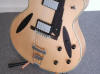
another look at the sound hole plugs. |
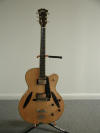 |
The plugs match the overall look of the
guitar, matching the rosewood finger-rest. |
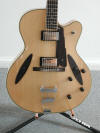 |
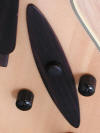 |
Here is a close up of the finished plugs.
When Joe came to pick up the guitar, we cranked up the loudest amp in the
shop to 10 - even with distortion - not an ounce of feedback. we had a
ball until the lawyer who occupies the office space next to the shop stopped
in to complain - oops. |
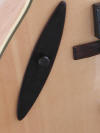 |